-
Shopping Cart (0)Cart Total:
Your cart is currently empty..
Knowlege --Outboard Motor
Top Cowling Design and Fabrication
- Tuesday, 13 February 2024
- 0
- 184
- 0
Top Cowling Design and Fabrication
The top cowling is an important part of the overall engine cooling system.top cowling Its main purpose is to provide air flow through the radiator (or other cooling device) to help prevent overheating of the engine cylinder heads. This flow of air is also responsible for cooling the oil in the engine.
As a general rule, the better the cowling is designed and fabricated, the cooler the engine will run.top cowling In fact, a properly functioning top cowling will help the engine operate at maximum efficiency under almost any load condition.
Unfortunately, no cowling is available on the market that will fit perfectly with every aircraft in which it is installed.top cowling As such, the individual airplane builder must develop and fabricate his or her own cowling for each project. This is especially true if the builder is using an engine that is not standard in size and/or type.
Cowling fabrication is not easy and requires a lot of skill.top cowling Developing a good accurate male mold over which to lay-up a fiberglass cowling is the hardest step in making one and is usually accomplished only after a great deal of time and effort. Once a good female mold is obtained, the cowling may be formed with glass cloth and mat until it has a thick rigid shell. After removing the cowling from the mold its internal surfaces must be carefully finished and any imperfections corrected. If not corrected, they will show up in the finish of all cowlings made from that female mold.
The most important considerations in designing a cowling for your particular airplane are the air inlet opening and the shape of the bottom portion of the cowling. The inlet opening needs to be located where it is best suited to provide sufficient flow of cooling air to the lower engine during climbs and nose high attitudes. Ideally, the cowling inlet should be shaped to form a nice rounded airfoil cross section so as to provide maximum cooling flow with minimum drag.
Depending on the type of aircraft and how the engine is to be operated, the bottom of the cowling may need to extend below the fuselage deck a bit in order to clear the alternator, starter, landing light or other items. If side gills are being used for cooling air exit, the cowling bottom profile will need to change its shape in order to blend smoothly with the fuselage contours on the sides.
Once the inlet and bottom of the cowling are shaped, a plywood jig should be built up on the front firewall area to support and align the cowling when it is being fitted. Small wood spacer blocks should be taped to the jig to establish the correct spacing between the cowling and the spinner. This spacing is needed to avoid the spinner rubbing against the completed cowling when the aircraft is in flight.
Another area of the cowling which is often overlooked is the method for securing the wires that feed electricity to the engine. If the ends of these wires are allowed to rattle around in the cowling they can be loosened and potentially disconnected during flight causing a dangerous condition. This problem can be avoided by securing the ends of these wires to the fuselage with appropriate hardware such as pan head stainless machine screws.
0users like this.
0comments
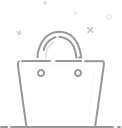
Your cart is currently empty.